3 Tips to Better Ground Control Points for Photogrammetry Projects
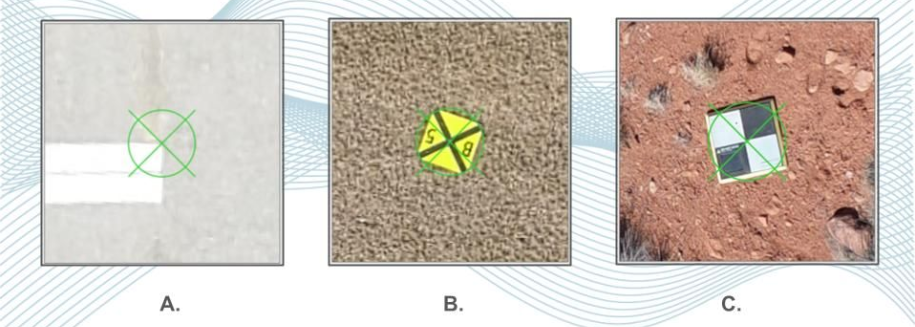
Why it is important to delineate ground control points (GCP) in photogrammetry
How a ground control point looks can have just as much impact as its placement throughout the project. Is it visible in comparison to its surroundings? Is it sized appropriately to be visible from the satellite, aircraft or drone sensor at altitude? Is it made of durable material, and has it been secured properly to ensure its use days or weeks after being set? Does it have a unique identifier or point number associated with it, and visible? Does it need to be reused over a long period of time? These are all things to consider and could affect the quality of your project schedule and deliverables. Below are three examples along with three tips to ensure the best results in choosing ground control points for satellite, aircraft and drone mapping.
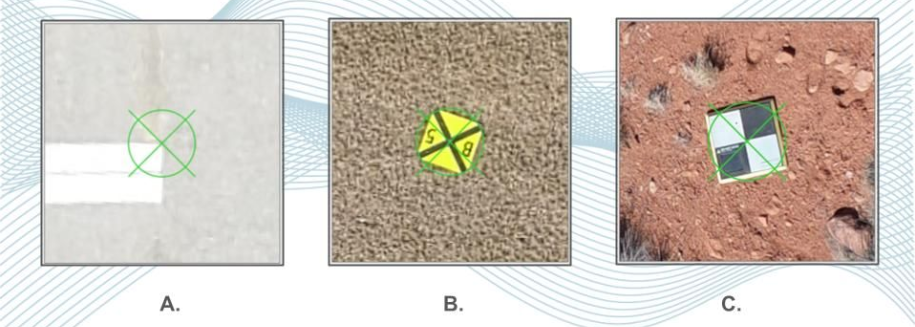
Different Types of Ground Control Points in Photogrammetry
Passive Ground Control Points
Passive targets (examples A & B) are the most common drone GCPs. A control point diagram is provided by a photogrammetrist or flight operations manager and they are set and surveyed by a field crew. Once surveyed the locations and elevations are provided to the photogrammetrist to use during the aerial triangulation (AT) process.
Active Ground Control Points
Active targets (example C) are a more recent type of ground control point seen primarily in drone mapping. These targets act as GPS receivers collecting their location information while the drone is flying its mission. Locations and elevations are then post-processed and provided to the photogrammetrist for use in the aerial triangulation.
In either case, the targets must be photo identifiable and in place before aerial data acquisition begins. They must remain in place until their survey, and the aerial acquisition has been verified as complete.
Tip 1. Ground Control Point Placement
One must be very careful with the ground control placement. This is particularly important with drone mapping as the aerial triangulation depends on many more tie points from many more images at a lower altitude. If a ground control point layout was provided and a given target's location is compromised by vegetation, move it so that it is no longer compromised. Only move it as far as necessary and confirm the new location with the person who designed the control point layout prior to establishing the new location.
This is also true for active targets that rely on GPS and a good network of satellites to capture a strong solution. Ensure these have a clear view of the sky as well as the horizon in the surrounding area.
Tip 2. Plan for Duration
Will your mapping project require multiple flights over a long period of time? If so, ensure the placement of your targets account for the activities being performed at the site. Is the project area an open field with wildlife or livestock? Livestock love to eat control point material. Will there be a lot of construction and grading? Avoid placing fabric or plastic targets in these areas. They may get run over before you complete the first aerial, satellite or drone survey. The same is true If you are using active targets: big yellow machines can roll right over active targets rendering them useless. Find locations within the project site or even better outside the project site where they will be undisturbed. Expand your flight if necessary.
If at all possible, use existing infrastructure. Paint, paint stripes, sidewalk cuts, directional arrows, and so forth are much more permanent than fabric or plastic, and with occasional refresh can last for years. With paint stripes use caution as they can be confusing to those in the office. Do not pick a generic stripe in the center of a parking lot, choose something less homogenous and/or more unique. For example, one that abuts up to an island or leads into an intersection with another.
Tip 3. Make your GCP Easily Identifiable
In many instances, the person processing photogrammetry data is not the person who collected it or did the field survey. There are a few things that can easily be done to make the process of locating targets much easier. Obviously good field notes are a starting point, but this doesn’t always happen. Create a targeting standard operating procedures (OP). Cover things like which side of a paint stripe, or at which point in an intersection of paint stripes measurements are to be made. Take photos of each point from a handheld camera or phone and provide these with the survey report. The easiest of all is to paint the ground control point number right next to it so that it can be easily read in the imagery and/or in a photogrammetry processing software such as SimActive’s Correlator3D product.
Additionally, consider the area around the target. White paint on concrete (example A) can be difficult to see with images that have blue from image motion. White targets in a field that still has snow can also be difficult to see. Use targets with opposing color schemes, black & yellow, black & white (examples B & C). Scale your control point to meet the sensor's altitude as well. A touch of neon can help with the point name or number, and even a drop right on the measured point itself can often be seen with drone mapping.
Conclusion
There are a lot of options when determining which control points you will use, where they are placed, and how they are delineated. The goal is to transfer the location and elevation of these control points efficiently to the person processing the data in the office with no room for misinterpretation. The tagging of the GCPs can also be facilitated and accelerated by using a higher-end photogrammetry software that includes a predictive algorithm. Such a function will allow you to identify a ground control point in one image, and then will automatically predict where in other images it will be located. The process will then only require the end-user to review if the predictions are correct. An example of such software suite is SimActive’s Correlator3D. For a trial license of Correlator3D please our free trial page.