There's more to accuracy than just an RTK/PPK enabled drone
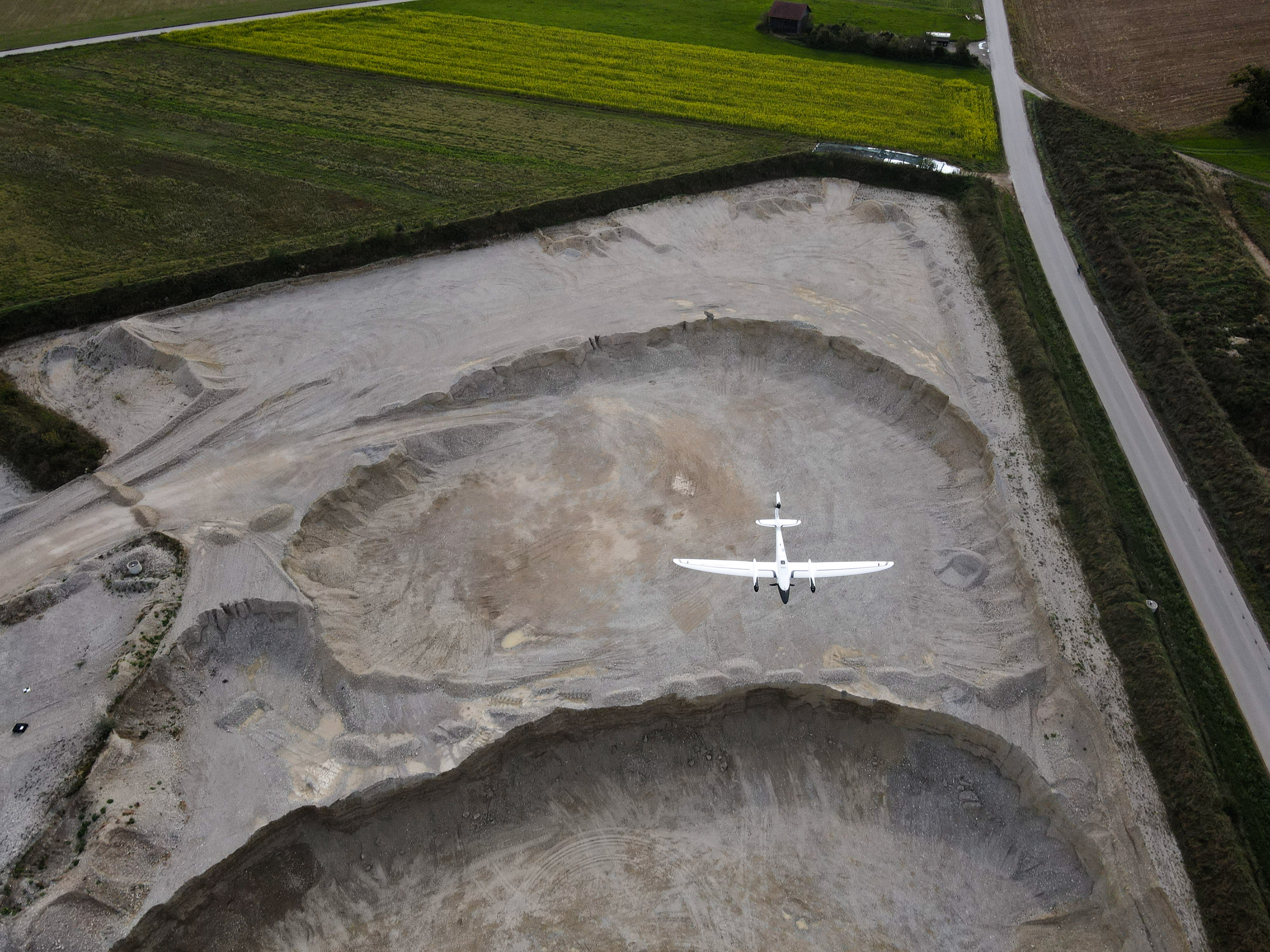
Real-time kinematic (RTK) and/or post processed kinematic (PPK) enabled drones are far superior to drones with just on-board GPS, right? A simple yes is a misconception as the real answer is more complicated.
RTK/PPK solutions are basically greatly enhanced GPS solutions. These give us the location (X, Y, Z) of each image. Photogrammetry has been used since long before any form of GPS, and still is today to produce highly accurate maps . RTK/PPK technology is often perceived as a solution that is much more accurate than a drone with just GPS. This is not necessarily true, as there are more factors that affect accuracy than accurate location measurements.
Three main things to consider
1. Photogrammetry solves for all errors
Given a handful of constraints, photogrammetry can solve for all errors through the aerial triangulation (AT) process. These include the physical size of the image/sensor, the focal length of the lens and orientation. Modern photogrammetry software such as SimActive’s Correlator3D can calculate the exact location of an image spatial position in relation to all other images through a bundle adjustment process. If ground control is added, the software will solve for the exact geospatial location of all images in relation to the surface below.
The accuracy of an image’s initial position may not be that important, given the additional sources of error such as orientation, and camera quality. Photogrammetry software can ultimately solve for all of these.
2. RTK/PPK enabled drones are part of a system that may still contain errors
Knowing that an accurate solution can be provided through photogrammetry and the AT process with the constraints listed above, what value then do RTK/PPK enabled systems provide? Most drones are already equipped with some form of low grade GPS. RTK/PPK do provide a higher quality GPS solution reporting positions in centimeters vs meters, but it is still an error that must be solved for.
Another potential source of error is in the image’s orientation at the time of exposure. This too must be solved for. This is done in one or two ways, through the photogrammetric process or with an extremely accurate inertial measurement unit (IMU). Finally, let’s not forget that most drone cameras are not metric and will need to be calibrated also through the photogrammetric process.
PPK was originally designed to be used in areas where it was not physically possible to survey in ground control. This could allow the owner of a PPK enabled drone the ability to capture and process reasonably accurate maps without control at all, where it simply cannot be provided. Capturing and processing a series of missions over a boresight with GCPs might allow the owner to calculate an estimated accuracy to be stated given certain conditions.
It is true that a better solution in the air from RTK/PPK enabled drones will give you a better solution, initially on the ground, meaning that the data processor will spend less time visually verifying control. This could also equate to fewer GCP’s as you become more confident with your system and the processing software.
3. Ground Control is the only true validation
Any responsible drone service provider knows that ground control is required to validate the mapping deliverables. This means that as provider, you will be spending time in the field setting control and doing some level of field survey, or at least contracting this task out. As stated above, one of the constraints needed in solving for geospatial position in the photogrammetric process is ground control. With an RTK/PPK enabled solution, these would be used as check points. Regardless of the quality of your drones onboard positioning system, survey should be performed to validate the results. If this is done, even with a low-quality GPS solution onboard the drone, photogrammetry can provide high accuracy mapping results.